With so many supplement makers in the market these days, how do they differ from one another? Why is picking a reputable supplement manufacturer important? Have you heard of supplement CDMO, aside from the more widely recognized terms supplement OEM and supplement ODM? A reputable supplement manufacturer can help you map out the worldwide market in addition to saving time and money when selecting the best private-label supplement manufacturer for your brand. As a result, you can service clients worldwide and make good money by working with supplement producers in the US and Asia.
This article provides a detailed analysis of supplement manufacturers, covering topics such as minimum order quantity (MOQ), common dosage forms of supplements, supplement suppliers, cost of manufacturing supplements, formulations of supplements, private label supplement manufacturers, and services that supplement manufacturers should offer to their clients.
What are the differences between supplement OEM, supplement ODM, and supplement CDMO?
The design process distinguishes between supplement OEM and supplement ODM.
Supplement CDMOs can provide in-house designs together with the appropriate production standards and manufacturing procedures, whereas supplement OEMs require brands to give and determine all supplement formulations, product specifications, and manufacturing processes.
OEM supplement: just provides manufacturing services.
Supplement ODM: is capable of developing and designing independently.
Provide in-house designs with the relevant production specs and manufacturing methods to supplement CDMO.
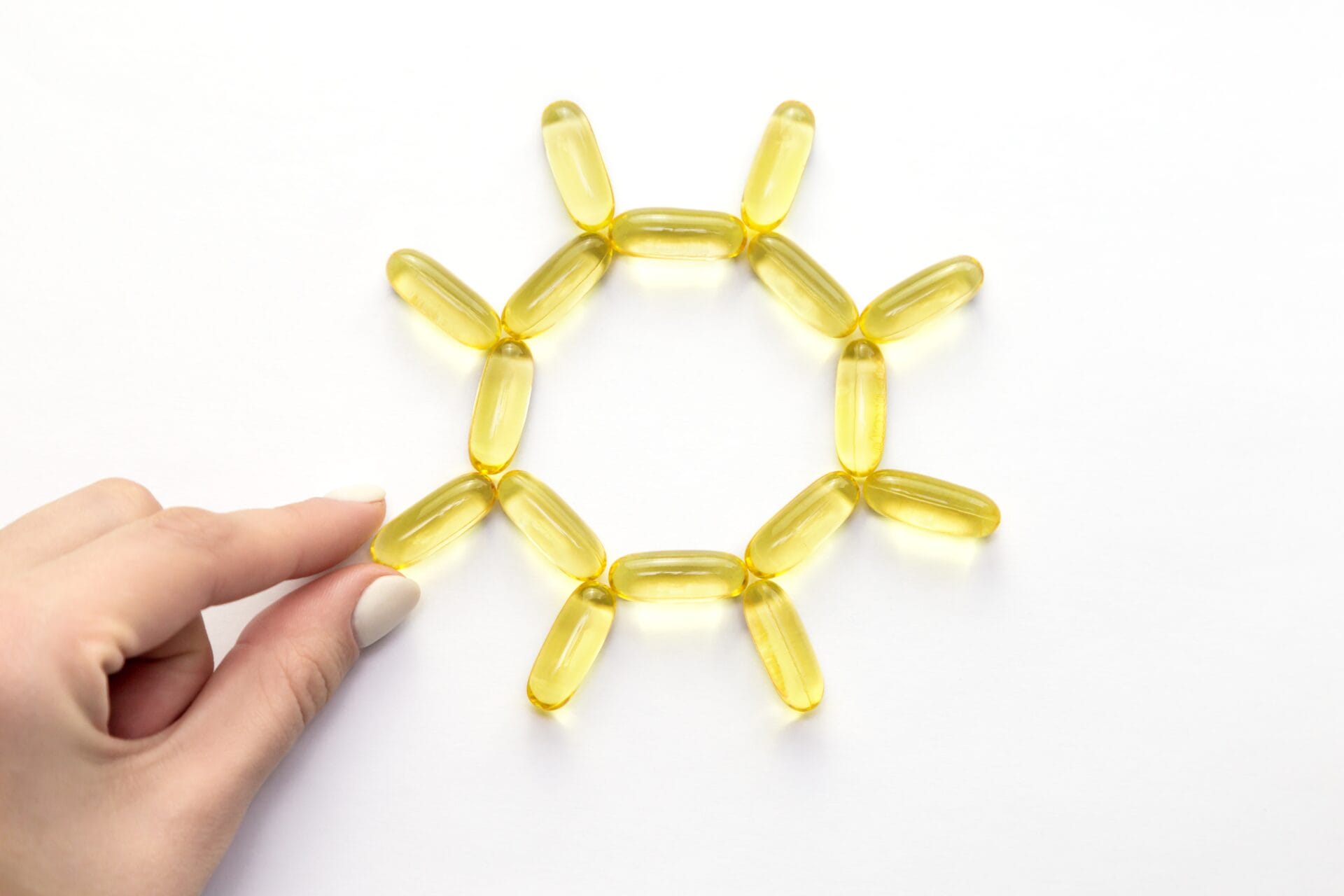
What is CDMO (Contract Development and Manufacturing Organization)?
The Contract Development and Manufacturing Organization, also known as CDMO, is an outgrowth of the more advanced out-of-the-box manufacturing service. It is possible to independently create and manufacture every component of a product, including the raw materials, the materials used for packaging, the providers of vitamins and minerals, and so on. You can create and manufacture your products, which gives you a competitive advantage in the market in terms of quality, flexibility, and time. This is the advantage.
As a result, there is a growing desire for private-label supplement companies to outsource their production to supplement contract manufacturing organizations (CDMOs) to reduce the amount of time spent on product research and production expenses, hence accelerating the time-to-market. Private-label supplement firms can devote more of their attention to marketing. Additionally, large-scale supplement CDMOs can tailor the location of product manufacturing to meet the requirements of the brand’s target market.
For instance, private-label supplement companies based in Europe have the option of selecting either a supplement producer located in Europe or one located in the United States. Supplement CDMOs, on the other hand, have a team of professionals with a variety of backgrounds who can design and manufacture products based on the requirements of the customer, the trends in local marketing, and the various types of private label supplements, which may include, but are not limited to, nutritional supplements, fitness supplements, and dietary supplements. These days, a growing number of private-label supplement companies make use of a supplement CDMO for outsourcing.
The outbreak of COVID-19 was the driving force behind the demand surge that reached a new height in the global market for biopharmaceutical products. A research report published by the International Research Institute (GII) indicates that the global CDMO market attained a value of $160.1 billion in the year 2020 and is anticipated to reach a value of $242.64 billion in the forthcoming year 2026.
The first thing you need to do is figure out who will be your supplement manufacturer. This will allow you to develop supplements of the highest possible quality and effectiveness, as well as the finest possible selection of different raw materials to employ. In addition to this, it is the most essential component of the production process. These are the fundamental components that make up a high-quality product. In the case of equipment, for instance, even the smallest flaws in the components will have an impact on the assembly process, which in turn will affect the overall quality of the final product.
The CDMO is capable of developing all of the raw materials for supplements on its own.
There must be a stringent selection procedure in place so that customers may feel confident about taking or using these supplements. There should be a collaboration between original equipment manufacturers (OEMs) of general food and raw material suppliers and supplement manufacturers that can meet the quality requirements and undergo inspections for heavy metals, preservatives, plasticizers, and other substances.
Developing raw materials is a significant area of focus for Supplement CDMO’s research and development efforts.
There is a growing willingness among supplement CDMO firms to engage in considerable research and development resources to find and create high-quality raw ingredients. They must ensure that their products are effective in addition to ensuring that they are of high quality and safe to use to distinguish themselves from other companies in the industry and become the finest private label supplement company.
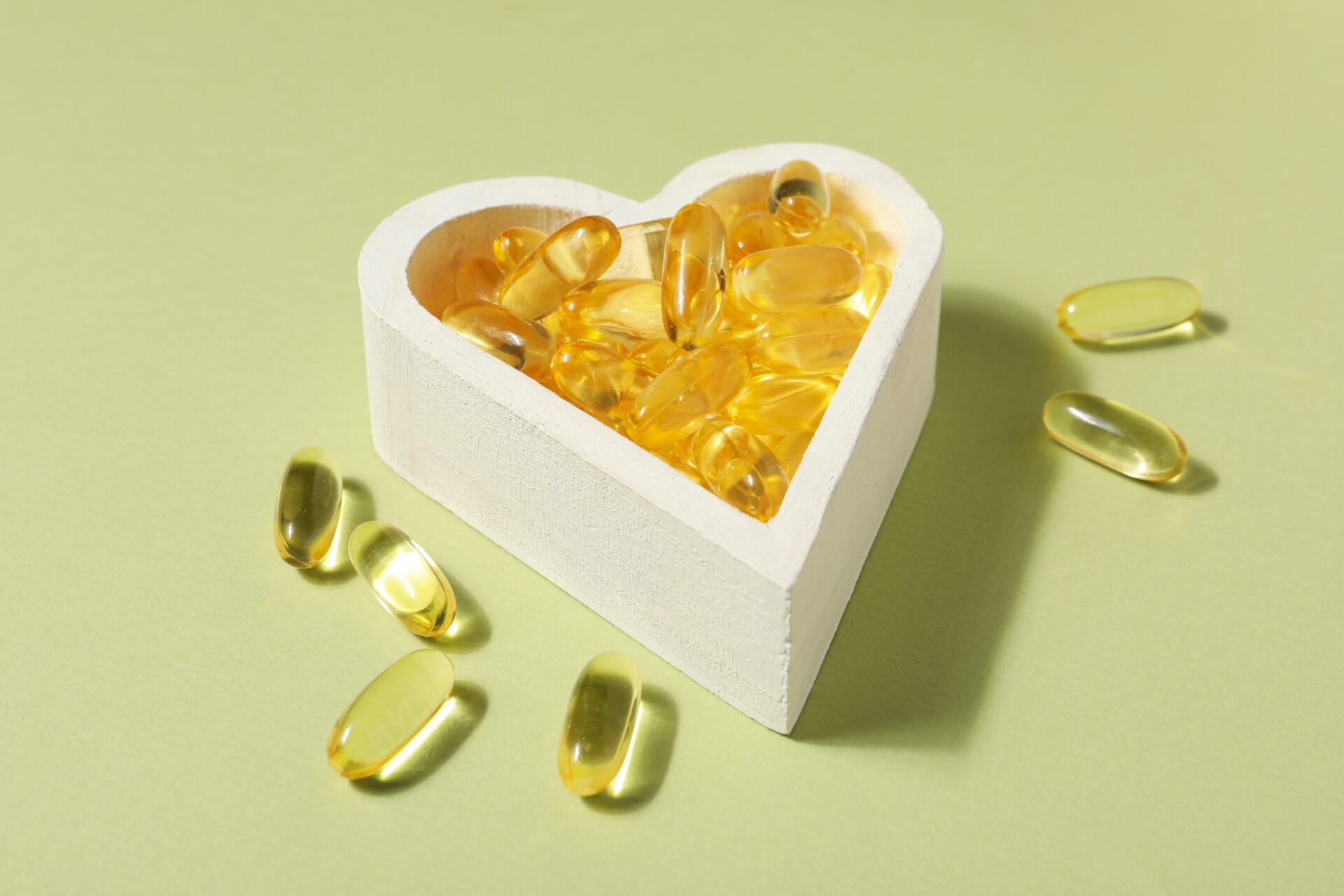
6 main development processes of supplement manufacturing
Supplement manufacturing involves several key processes to ensure the production of safe, effective, and high-quality dietary supplements. Here are six main development processes involved in supplement manufacturing:
1. Research and Development (R&D)
– Identification of Market Needs: The process starts with identifying market trends, consumer needs, and potential gaps in nutritional offerings.
– Ingredient Research: Extensive research is conducted on potential ingredients, their health benefits, and safety profiles.
– Formulation Development: Scientists and nutritionists work on creating formulations that meet regulatory standards and provide the intended health benefits.
2. Raw Material Sourcing and Testing
– Supplier Selection: Manufacturers identify and select reputable suppliers for raw materials, ensuring quality and compliance with regulations.
– Raw Material Testing: Raw materials undergo rigorous testing for identity, purity, potency, and contaminants to ensure they meet quality standards.
3. Quality Control and Assurance
– In-Process Quality Control: Throughout the manufacturing process, quality control measures are implemented to monitor critical points and ensure consistency.
– Final Product Testing: Finished products undergo comprehensive testing to verify the accuracy of the formulation, potency, and absence of contaminants.
4. Manufacturing Processes
– Blending and Mixing: Ingredients are combined in the correct proportions to create the supplement blend.
– Tablet/Capsule Formation: The supplement blend is transformed into the final product, either in tablet, capsule, powder, or liquid form.
– Encapsulation and Coating: For encapsulated supplements, the capsules are filled, sealed, and may be coated for easier swallowing.
5. Packaging and Labeling
– Packaging Design: Designing packaging that is not only attractive but also preserves the product’s integrity and freshness.
– Labeling Compliance: Ensuring that product labels adhere to regulatory requirements, including ingredient lists, nutrition facts, and health claims.
6. Regulatory Compliance and Documentation
– Compliance with Regulations: Ensuring that the supplement manufacturing processes adhere to local and international regulations such as FDA guidelines in the United States.
– Documentation: Maintaining detailed records of manufacturing processes, quality control measures, and testing results to demonstrate compliance and traceability.
7. **Distribution and Storage:**
– *Distribution Planning:* Developing a strategy for the distribution of finished products to retailers or directly to consumers.
– *Storage Conditions:* Establishing appropriate storage conditions to maintain the stability and quality of the supplements during transportation and on store shelves.
These processes collectively contribute to the development of high-quality dietary supplements that meet regulatory standards and provide consumers with safe and effective nutritional options. Manufacturers must continually adapt and improve these processes to stay abreast of evolving regulations and consumer expectations.